NEW Automotive / Engine Treatment - Roil
Gold
Revolutionary high performance automotive and cars engine treatment, an oil
additive, that reduces friction...
Test Results
There are a number of tests available to verify the characteristics of lubricating
fluids. They are carried out in accordance with specific industry standards that are
recognized worldwide.
Neways commissioned the
Queensland University of Technology (QUT) in Australia
to conduct the following tests, which conducted many times
previously, in
accordance with the American Society for Testing and Materials (ASTM) standards.
As the QUT carries out these tests for companies all over Australia, they cannot, for
obvious reasons, personally endorse any particular product they test. They do,
however, provide concise independent testing so consumers can form opinions on
an informed basis.
Test One: ASTM D3233B
Standard test method for extreme pressure properties of fluid lubricants (Falex pin
and vee block method).
A Falex test machine was used to conduct these tests. The test consisted of
running a rotating steel journal at 290 ± 10 rpm against two stationary V blocks
immersed in the lubricant sample. Load is applied to the V blocks by a ratchet
mechanism.
During the test, the load is increased in 250 lbf increments with load maintained
constant for one (1) minute at each load increment. The load fail value is obtained
at the point the test fails.
Neways provided the university with five samples for testing:
Sample A: A popular brand of mineral based oil.
Sample B: A popular brand of synthetic oil.
Sample C: A popular brand of additive mixed with mineral oil (sample A).
Sample D: Another popular brand of additive mixed with mineral oil
(sample
B).
Sample E: Roil Lower Engine Treatment mixed with mineral oil,
(sample
A).
As you can see from the test results (pictured), Roil proved itself to be an
outstanding product capable of handling extreme pressure and reducing friction.
The graph shows Sample E (containing the Roil Treatment) did not fail at 4,500 lbs
of true load. This was the maximum limit of the testing apparatus.
Test Two: ASTM D2783
Standard test method for measurement of extreme pressure properties of
lubricating fluids (Four ball method).
A Four Ball EP test machine is used for this test. It is operated with one steel ball
under load rotating against three stationary steel balls submerged in the test
lubricant.
The rotating ball moves at 1760 ± 40 rpm. The machine and test lubricant are
heated to 35° C, and then a series of tests, each of 10 seconds duration, are
carried out under increasing amounts of load until welding of the balls occurs. The
load at which the balls weld is recorded, as is the load wear index. This is
determined by the size of the 'scars' on the balls, which are measured under a
microscope-- the higher the index, the better the result.
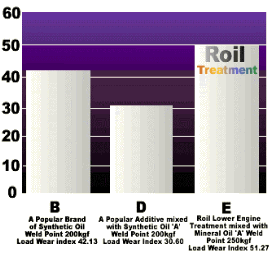
Neways asked the university to use the Four Ball test
on the three best performing
products from the Falex test.
Sample B : A popular brand of synthetic oil.
Sample D : Another popular brand of additive mixed with synthetic oil
(sample A).
Sample E : Roil Lower Engine Treatment mixed with mineral oil.
As you can see from the test results (pictured) Roil proved itself to be an
outstanding product capable of handling extreme pressure and reducing friction.
The graph shows Sample E (with the Roil Treatment) reached a weld point of 250
kgf with a load wear index of 51.27 kgf.